Now I am in this arrangement.
Everything has a very certian place to be. Due to homing positions after an emergency power-off situation, and tool change positions, and milling workspace, limits of the table movements, wires hitting or door hitting or ??
I cannot edit the homing "Dance" the mill wants to do. It is not to be changed from the way Haas wrote that code. Z retracts up first....then X-Y move to front-left of mill chamber together...then One rotary start spinning a certian way untill it finds home....then the Second rotary...
I had to work with the direction of rotation when mill is powered-on and homed for the first time, along with every possible combination of last coordinates for the axis to check for collision. I had major problems getting what I wanted into the mill. It was a real challange so far, but still working it out and moving forward. YEAH!
I think that we are very close to an idiot proof set-up. This is my goal. To be able to turn this machine over to an employee or even a kid and operate it safely. We will set limits for all axis, and try and come up with every bad situation we can think of now to see what happens. I am glad we are doing this, because we already found many many things that required a complete redesign over and over in the past few days. I think I have come up with the final solution to mill what I want.
So far, I have removed Two shields off the trunnion assemble and another cover on the bottom to expose and re-route the hydraulic lines and wires, this gave me more clearance on both ends, and I had to take apart the trunnion and re-assemble with one axis spun 60 degrees off from factory specs.
Have not had to use sledgehammer yet. Almost! But seriously....I NEED this to make teeth in Two weeks from now! All next week we calibrate and play with Renishaw toys, finish up the trunnion custom fixture to hold it to table sideways, then CAD of fixture design, then work with CIMSystem engineer the week after for

days to develope proper Post-processor and basic 5-axis strategys with my tools on this mill.
Maybe work with FDA on an alloy or Two? Get material tested, get machine verified and certified and blessed by Pope, and then make it Kosher and sell it!?
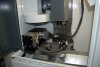