
DMC
Banned
- Messages
- 6,378
- Reaction score
- 260
We are ditching the Renishaw contact, length-only measurement system on our HAAS mills, and adding a custom made Laser tool presetter from Renishaw. I had Renishaw make me a small unit for our little Dental tools. Took them a Month to make for me.
It can measure Two different lengths and Two different diameter for crazy geometry tools.
<1um accuracy!
I am programming my HAAS to auto-compensate for smaller or larger tools than what we call for in the CAM.
This is perfect for diamonds milling Glass-Ceramics, and of course for Implants and bars.
Now we can change tools and tool manufactures without spending hours measuring to dial-in each stupid little tool to the single micron.
YEAH!!
Eat my shorts B&D Dental!
My mills are way more accurate than yours and much more flexible due to my fixture designs.
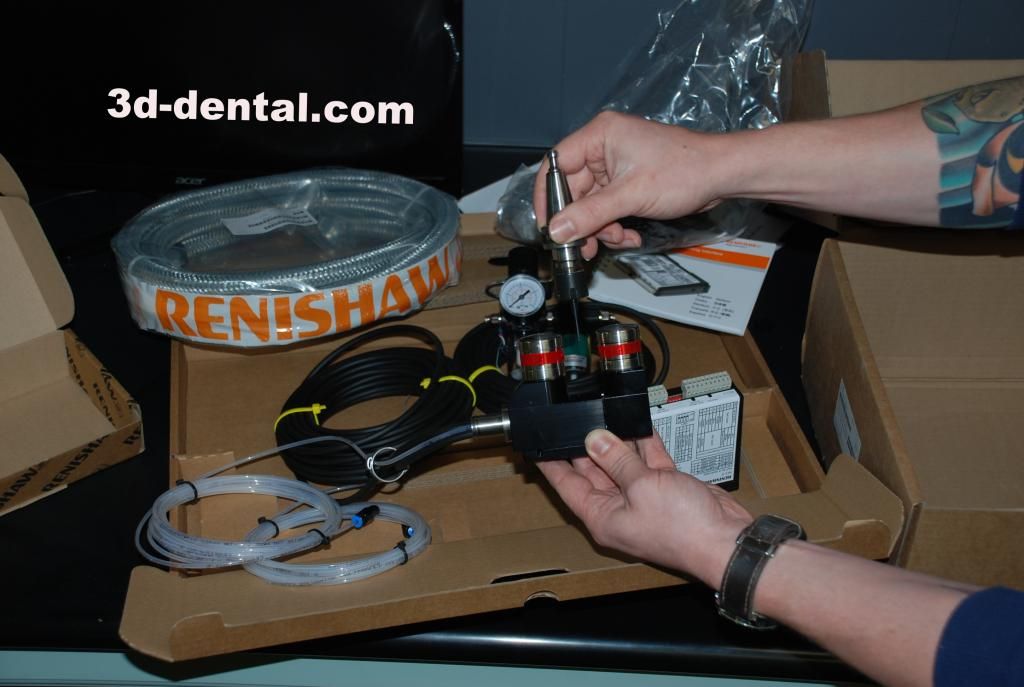
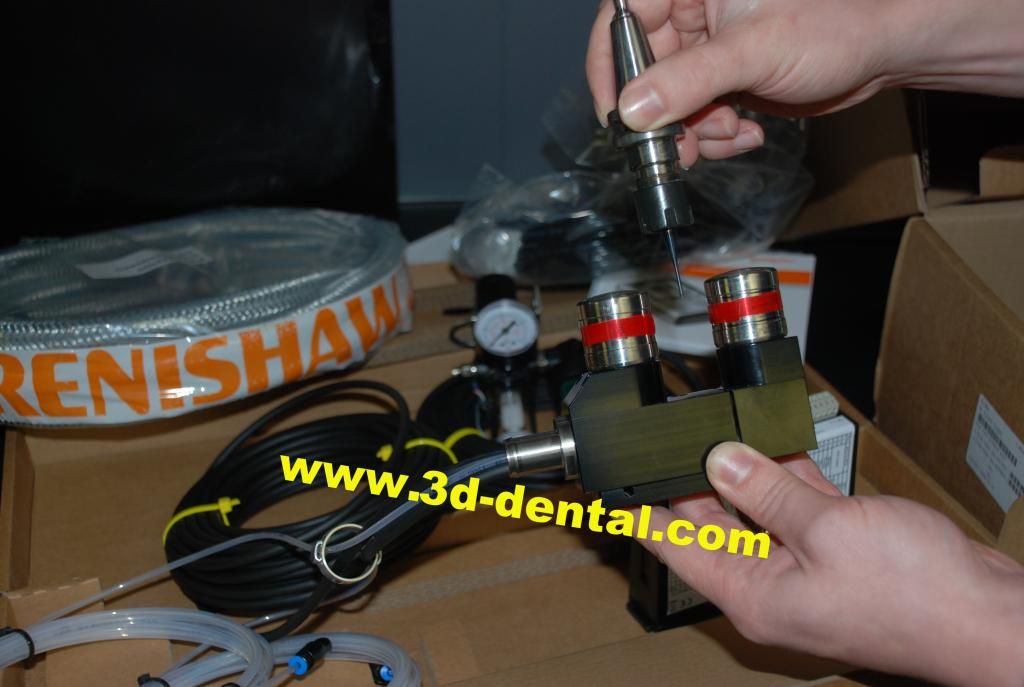
Getting rid of the table mounted Black probe as seen in this pic..
Mohammad, please resist the urge to post in this thread.
It is over your head! LOL
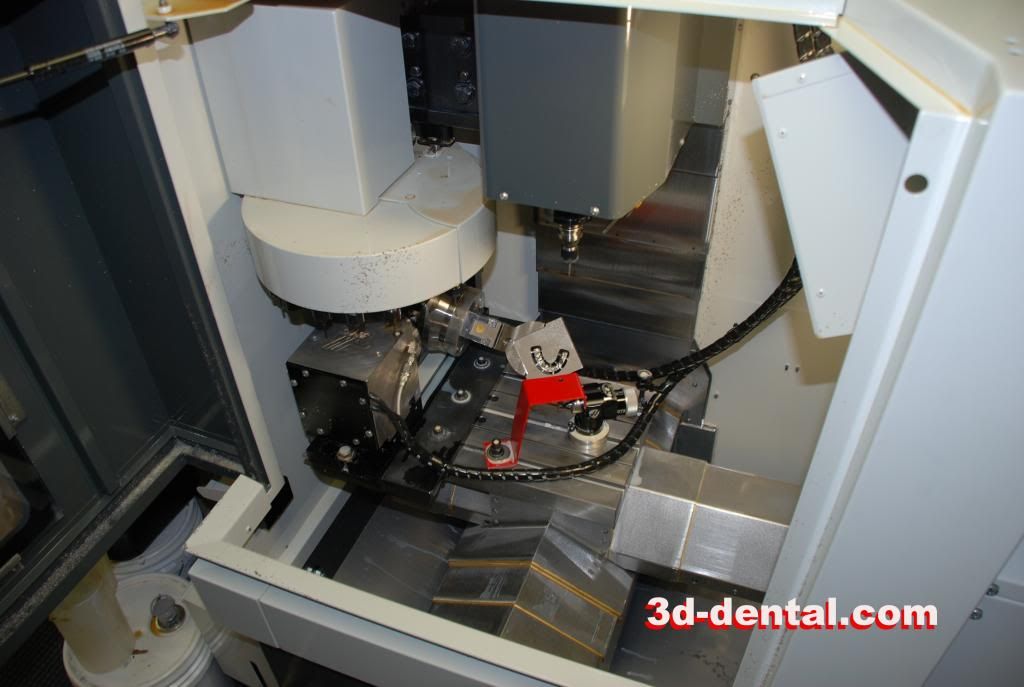
It can measure Two different lengths and Two different diameter for crazy geometry tools.
<1um accuracy!
I am programming my HAAS to auto-compensate for smaller or larger tools than what we call for in the CAM.
This is perfect for diamonds milling Glass-Ceramics, and of course for Implants and bars.
Now we can change tools and tool manufactures without spending hours measuring to dial-in each stupid little tool to the single micron.
YEAH!!
Eat my shorts B&D Dental!
My mills are way more accurate than yours and much more flexible due to my fixture designs.
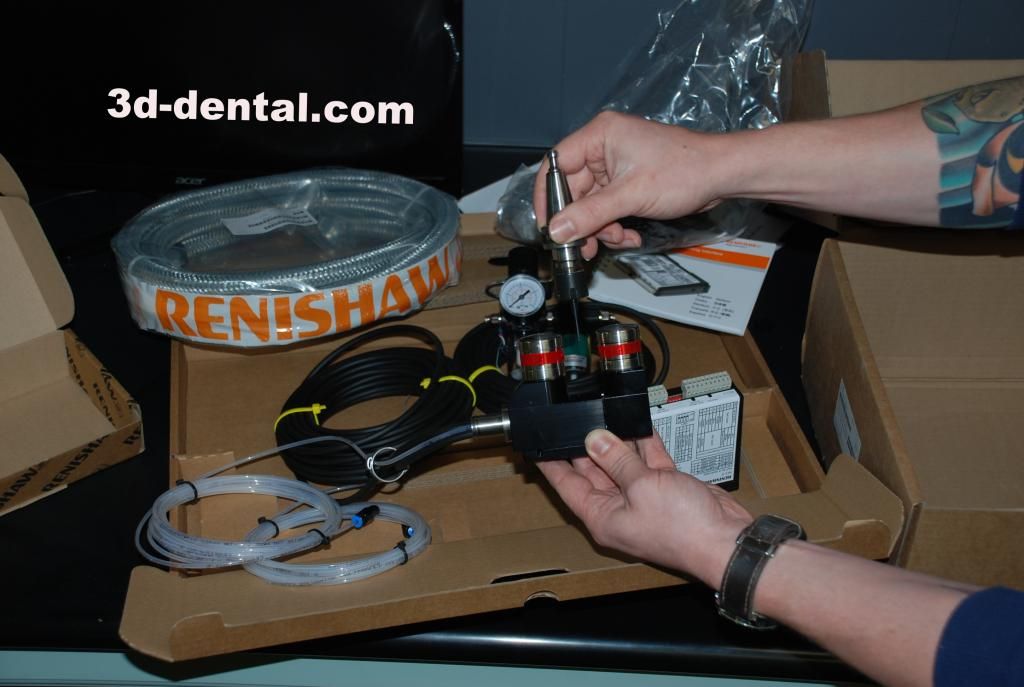
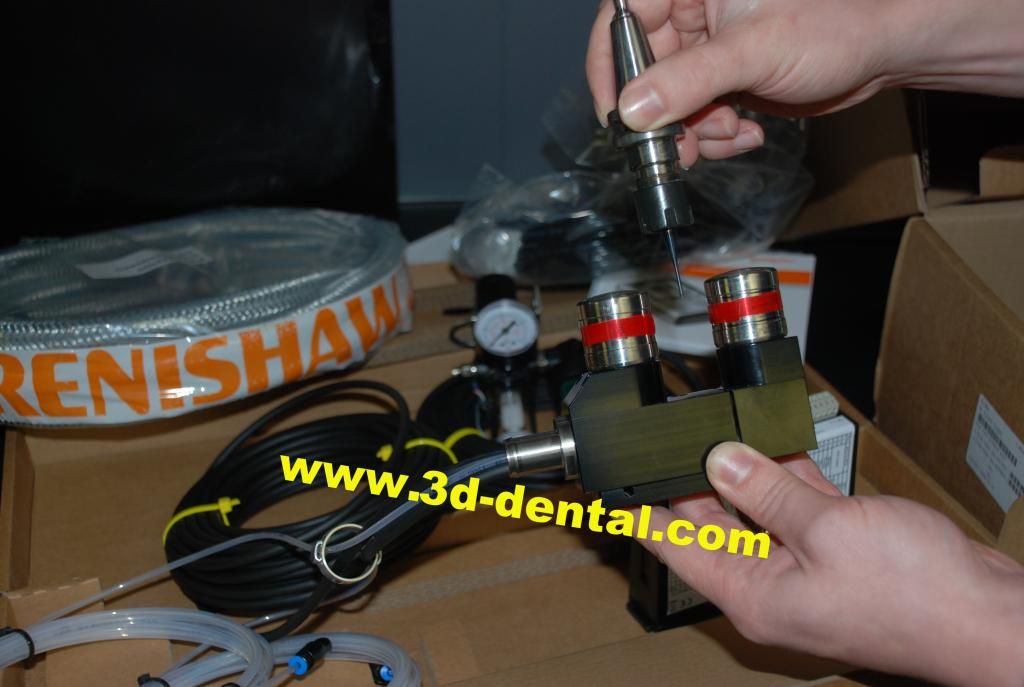
Getting rid of the table mounted Black probe as seen in this pic..
Mohammad, please resist the urge to post in this thread.
It is over your head! LOL
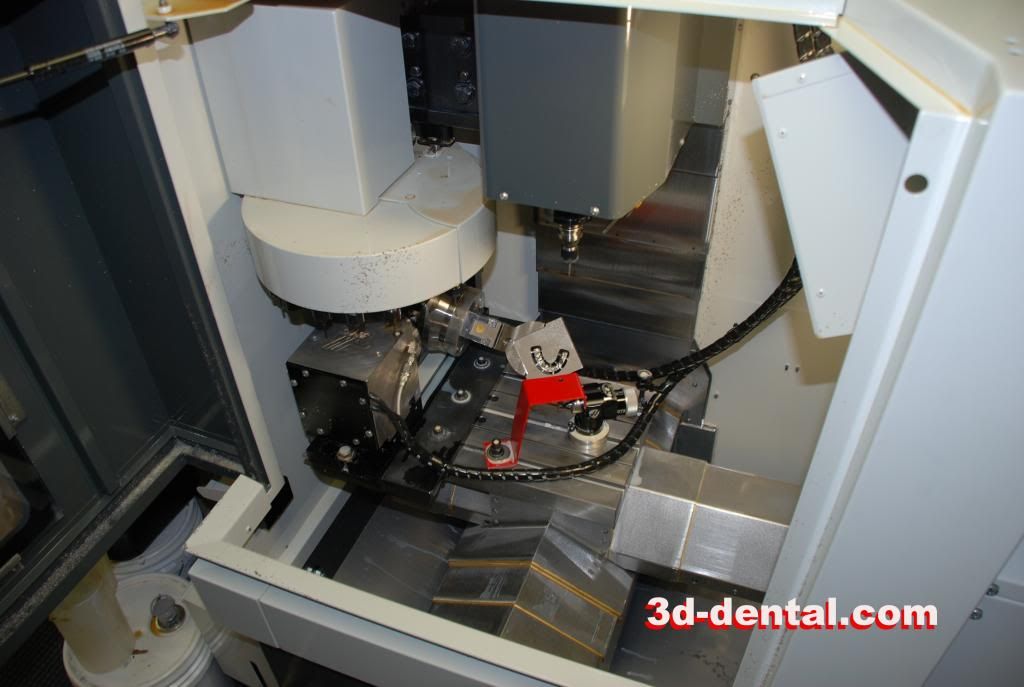